OEE(設備総合効率)とは?計算方法・改善要因・改善方法を解説!
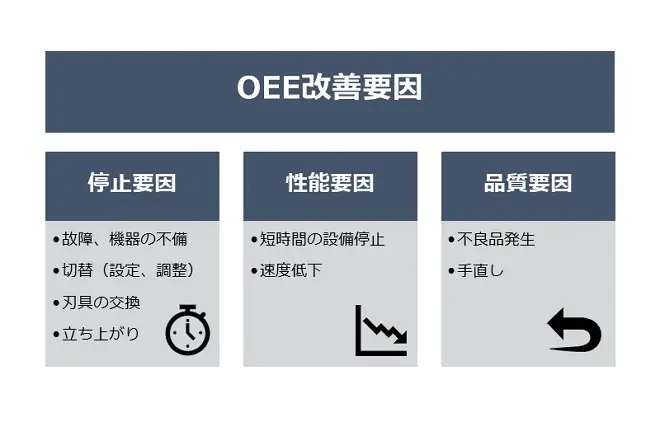
OEE(設備総合効率)とは何か?
OEEとは設備総合効率(Overall Equipment Effectiveness)のことで、生産設備の効率を表す指標です。
最大限の生産能力に対して、生産設備がどの程度稼働しているのかを表しています。製造現場で用いられる、リーン生産方式や全員参加の生産保全(Total Productive Maintenance, TPM)においてもOEEは重要な指標の一つです。
OEEでは「発揮されていない生産能力」を取り戻すために、製造過程の「大きなロス」に着目します。つまり、OEE改善とは、ロス低減による生産能力向上を意味します。
OEEの計算方法
OEEは、以下の式で表されます。
OEE(設備総合効率)=時間稼働率×性能稼働率×良品率
①時間稼働率の求め方
時間稼働率は、
時間稼働率=稼働時間/負荷時間=(負荷時間-停止時間)/(総合時間-計画停止時間)
と表されます。
例えば、下記の図1のケースでは、
図 1:生産履歴サンプル
負荷時間
負荷時間=総合時間-計画停止時間=9時間-1時間=8時間=480分
- 総合時間:OEEのを計算対象となる時間帯です。例では8:00~17:00のOEEを計算したいので、9時間となります。
- 計画停止時間:生産計画を入れない時間帯です。休憩や設備の計画保全が対象となります。図1のケースでは昼休みの1時間が該当します。
稼働時間
稼働時間=負荷時間-∑停止時間=480分-(10分+35分+12分+20分+15分+45分)=480分-137分=343分
- 停止時間:「設備故障」「段取り替え・調整」「刃具交換」「立上げ準備」などの生産効率の低下要因になっている時間です。これらの停止時間の総和を計算します。
結果として、
時間稼働率=稼働時間/負荷時間=343分/480分=約71.5%
となります。
②性能稼働率の求め方
性能稼働率は、
性能稼働率=正味稼働時間/稼働時間=(基準サイクルタイム×加工数量)/稼働時間
と表現されます。基準サイクルタイムが60秒(1分)とすると、
性能稼働率=正味稼働時間/稼働時間=(基準サイクルタイム×加工数量)/稼働時間=(1分×300個)/343分=約87.5%
となります。
③良品率の求め方
良品率は、歩留まりと表現されることもありますが、加工総数における良品数の割合を示す指数です。例えば、300個の加工品の内で、不良が3個発生した場合は、
良品率=良品数/加工数=(加工数-不良数)/加工数=(300個-3個)/300個=99%
となります。
したがって、この上記ケースの場合、OEEは下記の値となります。
OEE(設備総合効率)=時間稼働率×性能稼働率×良品率=約71.5%×約87.5%×99%=約61.9%
となります。改善余地が結構ありそうなOEEです。
OEEの改善(ロス低減)要因
OEE改善のためには以下3つの要因(ロス)に焦点を当てる必要があります。
- 停止要因:設備故障、段取り替え(設定、調整)、刃具の交換、立ち上がりなどのロスのこと
- 性能要因:短時間の設備停止(チョコ停)や速度低下によるロスのこと
- 品質要因:不良品発生や手直しによるロスのこと
OEEの改善方法
OEEの改善活動は対処と予防の2つに分類することができます。
問題への対処は、問題の発生を迅速に知り、素早く対応し、ロスを最小限に抑えることが大切です。問題を素早く認識するためにはリアルタイムデータの取得が効果的です。また、問題解決後は再発予防が欠かせません。予防のために、品質保全や改善活動を実施します。そして、優良な工場では以下の2つの「改善」が行われます。
①現場改善 | ②システム的改善 |
現場改善の強みは、問題があることに気が付いたら、すぐにそれを解決し、効果確認できることです。現場改善の多くは、現場での作業者や技術者の五感による気付きによるものであり、比較的に大きな投資も必要ないため実施しやすいです。しかし、革新的な改善となる可能性は低いです。 | システム的改善は、問題の根本的な変革や改善のことです。システム的改善には、潜在的な問題を「見える化」することが必要であるため、一定期間以上の詳細で信頼できるデータ収集とデータ分析が欠かせません。 |
OEEの改善にはMES導入が有効
上記のような改善文化の構築・維持のために、必要な「目標や指標」と「現状」の差の可視化が重要です。そして、生産現場の重要な指標の1つであるOEEを算出するためには停止時間やサイクルタイムのデータが必要となります。
アナログな方法 | MESを活用する方法 |
OEEを算出するアナログな手法としては、これらのデータを取得するためには停止時間と理由を人海戦術で調査/記録したり、実際の作業をカメラで録画して分析したりすることも可能ですが、現状把握のために多くの工数が必要になります。さらに、このような方法では、データの正確さは、測定・分析する人に依存してしまいます。 | OEE算出のために、MES(製造実行システム)の導入が可能であれば、これらのデータは自動で収集可能となります。また、収集されたデータは自動的に蓄積されるので、任意の期間でOEEを自動計算することが出来ますし、傾向管理や過去データとの比較が容易に出来ます。複数台の生産設備を対象にOEEを計算することも可能であるため工場全体のOEEをリアルタイムでモニタリングすることが可能となります。 これまで作業者や作業長が報告書作成のために費やしていた時間を、MESを利用してオンライン、リアルタイムの情報を把握することで大幅に削減出来ます。また、ロスの量、発生時間、発生頻度、関連する可能性のあるパラメータなどのデータを収集、分析することで、効果的に問題の原因究明が可能になります。 このように、MESを導入することで、素早く効果的な継続的改善活動が可能になります。 |
製造実行システム(MES)ProManage Cloudのご紹介
弊社は、製造実行システムの導入実績が豊富なProManage社( 本社: シカゴ)が開発販売する「製造実行システム(MES)ProManage Cloud」をご提案しています。
「ProManage Cloud」であれば、様々な生産設備から自動でデータを収集することで、報告書の作成やパソコンへの入力作業などの工数を最小限に抑えて、信頼できるデータ収集ができます。
収集したデータを利用して、OEEに関するレポートはじめ、ロスの改善や問題の未然防止に役立つ様々なレポートを自動生成します。
また、所定の時間にメールでレポート配信することや、スマホの専用アプリを使用してリアルタイムで対象設備の稼働状況やOEEを確認することも可能です。
生産管理のKPIとしての「ISO22400 」にも準拠しているので、社内外の同一設備や工程の実力を客観的に比較評価することも可能です。
ProManage Cloudについて、詳しくは下記リンクからご覧ください。
https://factory.itnet.co.jp/solution/promanage
※ISO22400は、業種、業態、企業で統一性が無かったMES領域の評価指標を標準化したものです。日本やアメリカをはじめ、ドイツ、フランス、スウェーデン、スペイン、韓国、中国などがこの取組みに参画しています。
Supporting Problem Solving
Supporting Problem Solving
Supporting Problem Solving
Supporting Problem Solving